What is Porosity in Welding: Usual Sources and Effective Solutions
What is Porosity in Welding: Usual Sources and Effective Solutions
Blog Article
The Scientific Research Behind Porosity: A Comprehensive Overview for Welders and Fabricators
Comprehending the detailed mechanisms behind porosity in welding is essential for welders and producers making every effort for impeccable workmanship. From the composition of the base products to the intricacies of the welding procedure itself, a wide range of variables conspire to either intensify or reduce the presence of porosity.
Recognizing Porosity in Welding
FIRST SENTENCE:
Assessment of porosity in welding discloses important insights into the stability and high quality of the weld joint. Porosity, defined by the presence of cavities or spaces within the weld steel, is an usual worry in welding procedures. These spaces, if not properly resolved, can compromise the architectural stability and mechanical homes of the weld, causing possible failures in the ended up item.

To detect and evaluate porosity, non-destructive screening approaches such as ultrasonic testing or X-ray inspection are usually employed. These techniques allow for the recognition of interior defects without endangering the integrity of the weld. By examining the dimension, shape, and circulation of porosity within a weld, welders can make informed choices to enhance their welding procedures and achieve sounder weld joints.
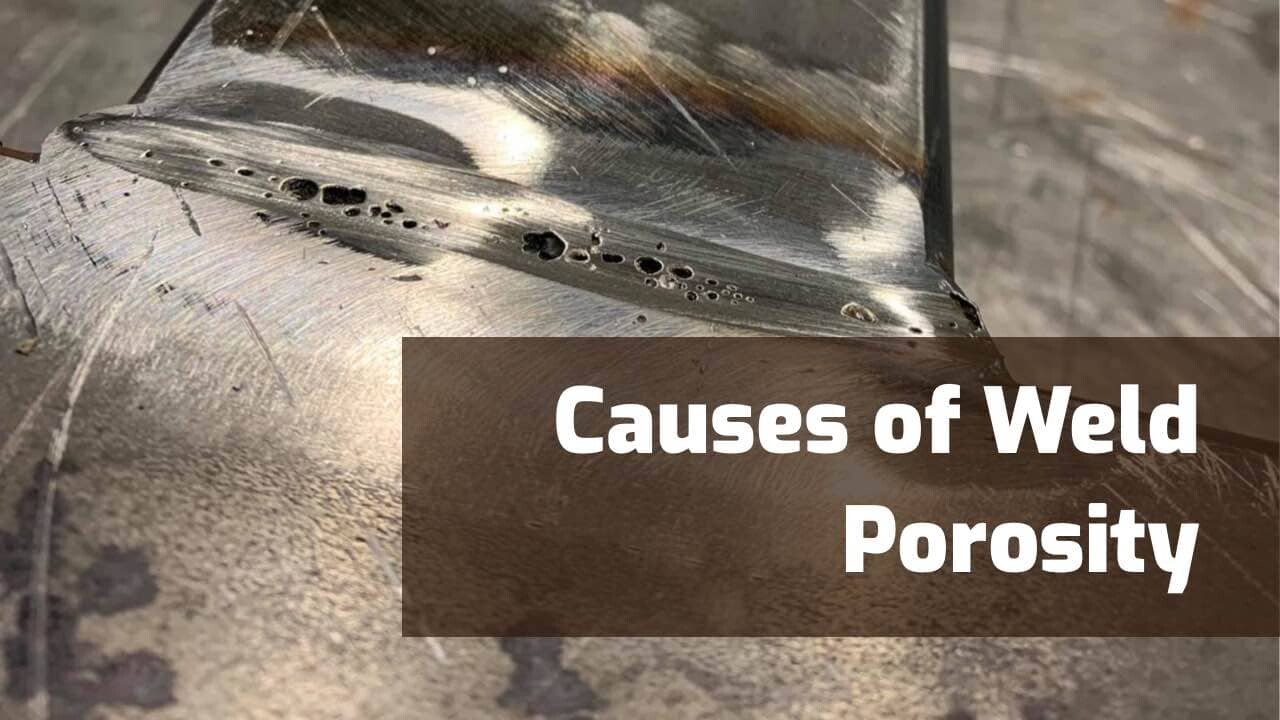
Aspects Affecting Porosity Formation
The occurrence of porosity in welding is influenced by a myriad of variables, varying from gas shielding effectiveness to the complexities of welding criterion settings. Welding specifications, including voltage, present, travel rate, and electrode kind, likewise impact porosity development. The welding strategy utilized, such as gas metal arc welding (GMAW) or secured metal arc welding (SMAW), can affect porosity formation due to variations in heat circulation and gas protection - What is Porosity.
Impacts of Porosity on Weld Quality
The existence of porosity also deteriorates the weld's resistance to corrosion, as the caught air or gases within the spaces can respond with the surrounding atmosphere, leading to deterioration over time. Furthermore, porosity can hinder the weld's capacity to withstand pressure or influence, additional threatening the overall high quality and integrity of the bonded framework. In essential applications such as aerospace, vehicle, or architectural buildings, where safety and security and resilience are critical, the damaging effects of porosity on weld top quality can have severe effects, try this emphasizing the importance of lessening porosity with appropriate welding techniques and treatments.
Methods to Decrease Porosity
Furthermore, making use of the ideal welding parameters, such as the appropriate voltage, existing, and travel speed, is vital in stopping porosity. Preserving a regular arc length and angle during welding likewise assists minimize the possibility of porosity.

Making use of the ideal welding technique, such as back-stepping or employing a weaving activity, can likewise help distribute warmth evenly and decrease the opportunities of porosity development. By implementing these techniques, welders can efficiently decrease porosity and create high-quality bonded joints.
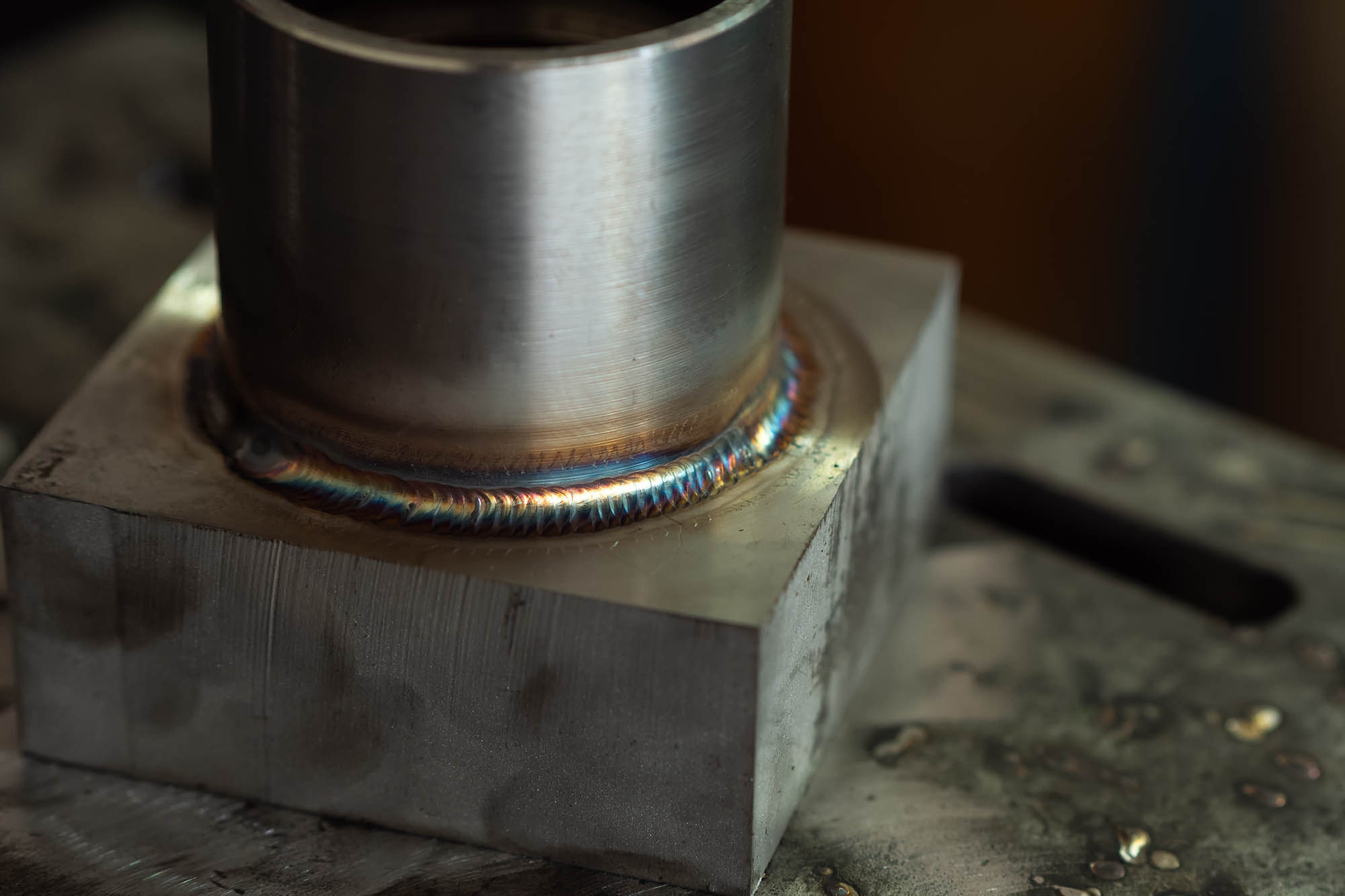
Advanced Solutions for Porosity Control
Carrying out cutting-edge innovations and cutting-edge approaches plays a crucial function in achieving remarkable control over porosity in welding processes. Furthermore, utilizing advanced welding strategies such as pulsed MIG welding or customized ambience welding can additionally aid alleviate porosity concerns.
One more innovative option entails making use of sophisticated welding devices. Using equipment with integrated features like look at this now waveform control and sophisticated power sources can improve weld high quality and reduce porosity risks. The execution of automated welding systems with accurate control over specifications can substantially decrease porosity defects.
Additionally, integrating advanced tracking and assessment innovations such as real-time X-ray imaging or automated ultrasonic testing can aid in discovering porosity early in the welding procedure, permitting for instant corrective activities. Generally, incorporating these sophisticated options can significantly improve porosity control and enhance the general high quality of bonded components.
Final Thought
In conclusion, understanding the science behind porosity in welding is necessary for welders and producers Learn More to generate high-grade welds - What is Porosity. Advanced remedies for porosity control can further enhance the welding process and guarantee a strong and trustworthy weld.
Report this page